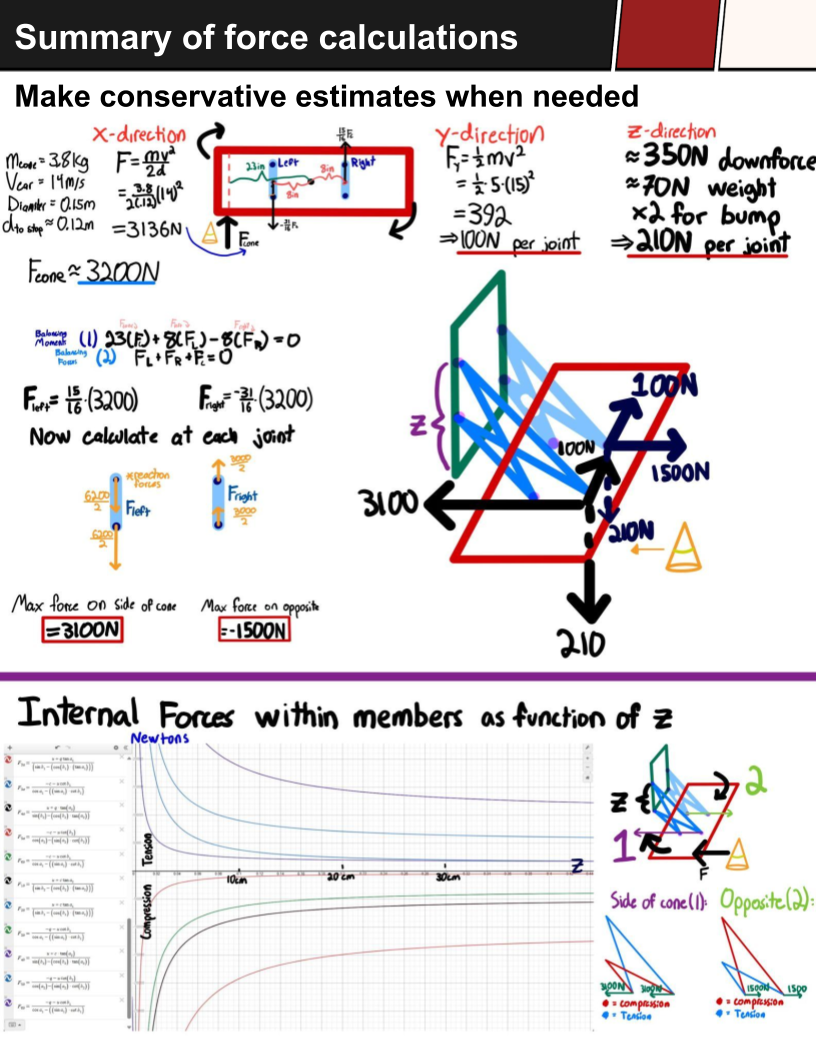
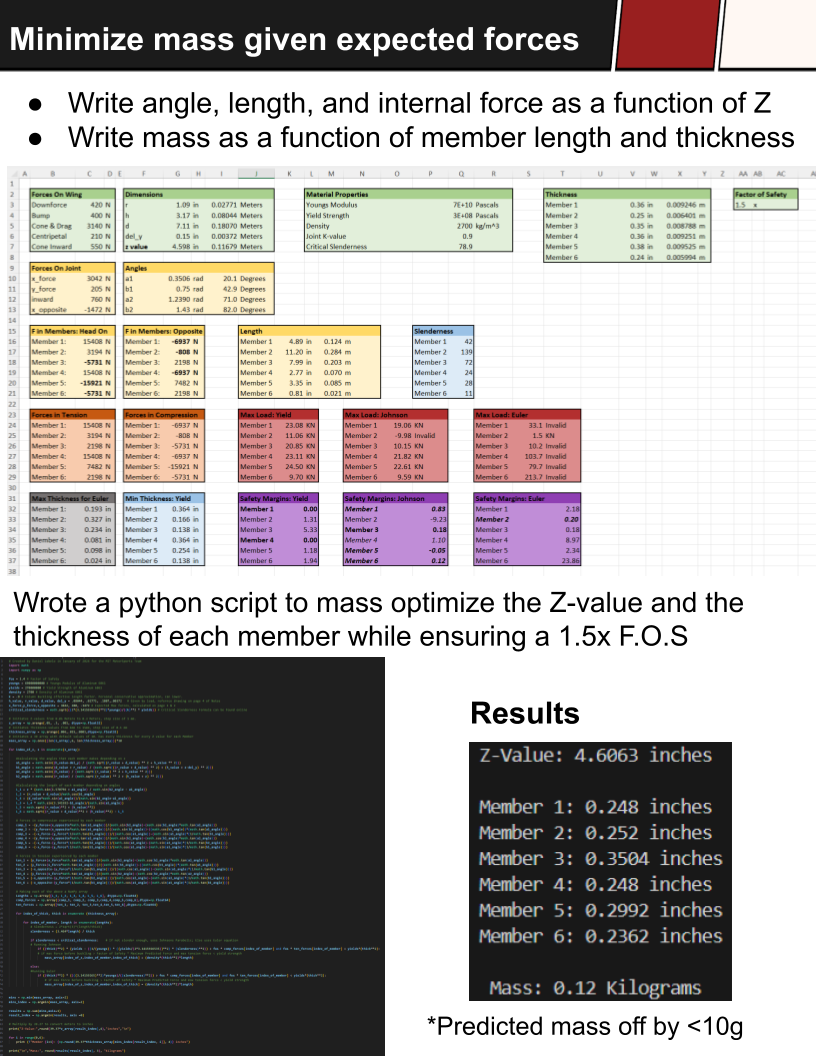
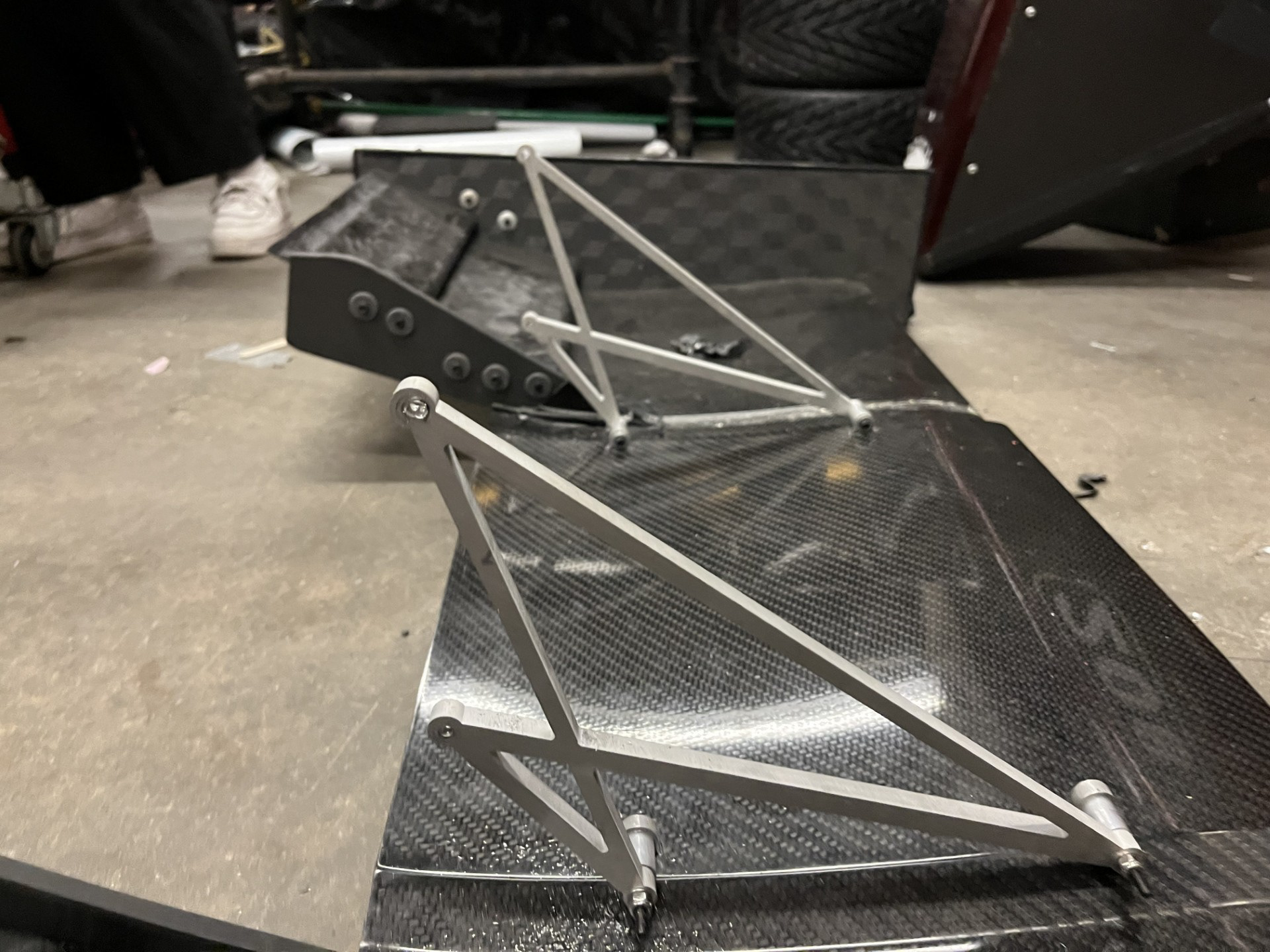
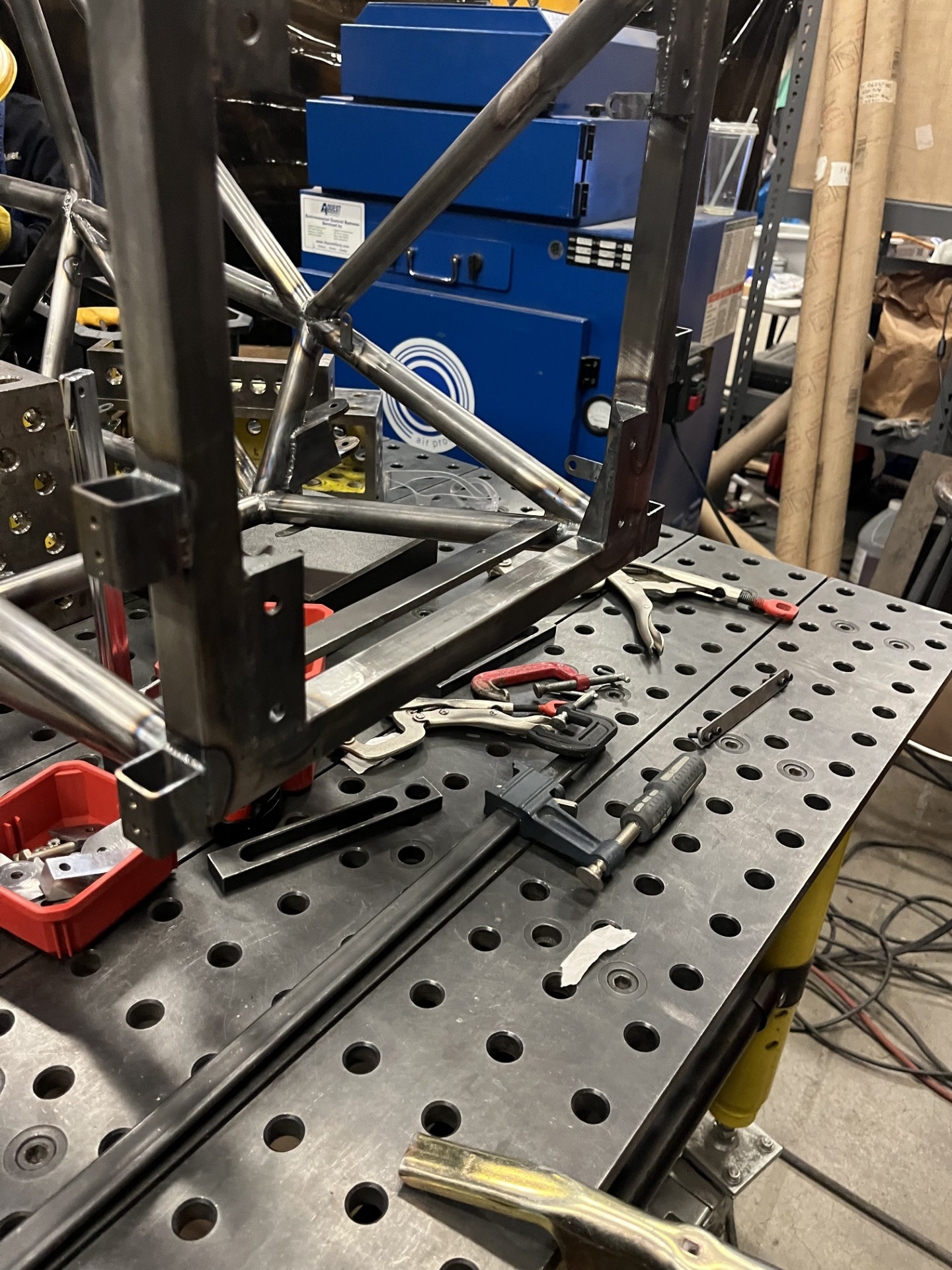
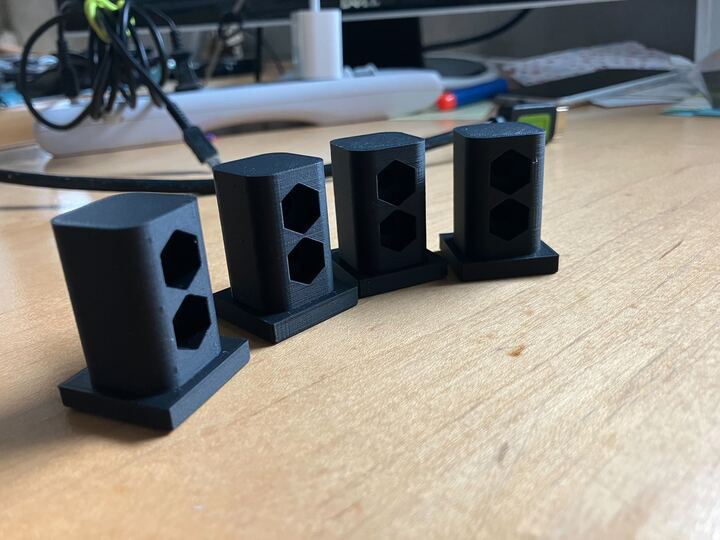
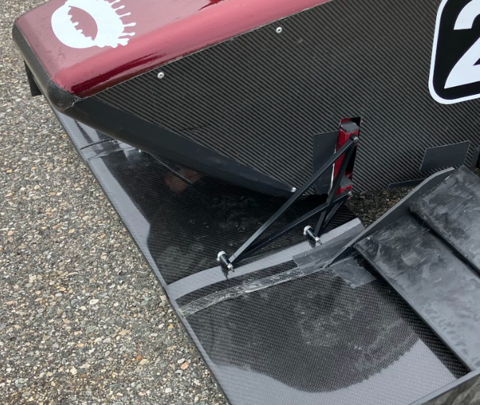
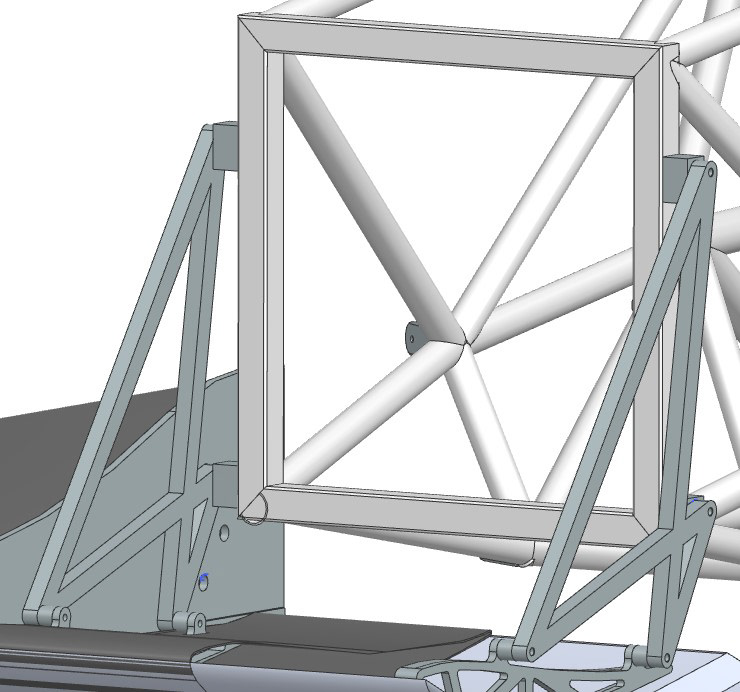
Objective: To design and build the lightest mount possible while ensuring a 1.5x factor of safety under various calculated loads.
Responsibilities & Collaboration:
I was responsible for creating a mounting mechanism that connects the front wing to the frame of the car. I worked closely with the Mechanical lead and the Aerodynamics lead of the team to ensure that it satisfies the needs of both subsystems. I learned about manufacturing, hand calculations, NX, NX CAM, and much more by asking around and attending "lessons" taught by experienced members. I also learned many skills on my own time through YouTube, various websites, and a college textbook. Ultimately, this project taught me how to diligently work on my own project but without fear of asking for help or using my resources.
Outcomes:
After putting a few ideas into a design matrix, I ultimately decided on a truss-like design. Modeling the member as an ideal truss simplified calculation. Failure now depended on length, thickness, material, and internal load (which is dependent on forces to wing and geometry of the members). My designs were constrained to those which could withstand 1.4x the predicted loads. This makes it more difficult to mass optimize since writing a 'traditional' optimization equation would yield 0in thickness as it's the lightest solution. My attempt to create a set of equations that could minimize mass while accounting for this proved too difficult as I had 9 variables to control (material, 2 position ones and 6 thickness ones) and many were interwoven with each other. For this reason, I created a script which simply ran through every combination, discarded those which weren't strong enough, and then returned the lightest configuration left. Once I had the parameters, I designed it in NX and then manufactured it. It was then powder coated and mounted on the car.